Quote:
Originally Posted by cturbo28
See above post on WG answer. On the exhaust, I really do not know if welding the two different types hurt anything but I have not had any problems so far. the breakdown of the material is this.
1. Manifold 321ss
2. 3" vband 304ss
4. 3" to 3.5 transition 321ss
5. DP 3'5" 321ss
6. flex joint 304 ss
7. 3.5 to 4" transition 321ss
8. 4" straight section 26"s, 321ss (removable to be straight or Magna flow)
9. 4" from #8 back to Magna flow in rear 409ss
My plan was to run 20 ga. 321 all the way back but it was hard to justify the cost to material advantage.
On the IC, my intake temps get a little high. 145F-175F range during a race on a 90+ degree days. Not sure if it is the IC or the nature of the beast. I usually run 19-21psi so the intake temps get up there. The example I pulled up happened to be a little cooler day might have been 80 degrees at the most. not really sure.
The stock twins are no comparison to the single I have on it now. Best way I can explain it is it would be the difference in a C6 Z06 compared to a stock RX-8.
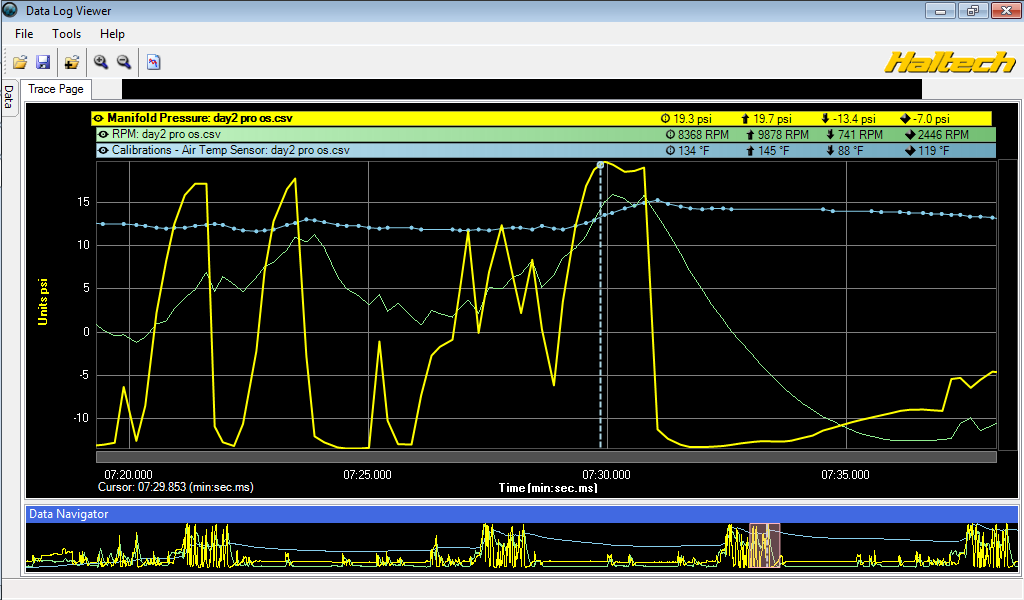
|
OK gotcha, so you already made a heat shield and still doesn't help. Well, shit. I guess water and/or relocation is the only choice then. Have you ever wrapped the DP as well to try to help with that or is it against the rules?
I'm not sure how you kept all those materials and locations straight in your mind haha, but thanks for the info! I thought you went straight from the Vband on the turbo to a 4" DP. Gotcha. And I can completely understand not doing the whole thing in 321ss, not worth the benefit vs cost. Was there a specific reason you got an RB flange? Someone else suggested getting that one too but I don't yet know why. I'll get it anyway though, no biggie.
As far as the cooling efficiency of the IC, I've never measured my temps so I wouldn't know how they compare to yours, but I know current VMIC works pretty well as far as cooling. I just think I might be able to get less pressure drop with something with smoother flowing end tanks. Then comes the problem of the air moving too fast to be cooled efficiently...and for that I was going to use 2.75" exit and 3" entrance piping. But flow/CFM is where I'm stuck right now. Not that it really matters, I'm not racing, just trying to give my all to build my favorite street car haha. MAYBE it'll see the track someday, but I've never paid attention to rules and regulations so I'm so far past it now and it's not worth going back.
So you're saying the single responds faster than the stock twins? Or are you talking just about the power it delivers? I didn't think any single would respond as fast as the twins. I was hoping short runners and an efficient IC would help though.
Sorry for all the questions, but thanks for responding anyway.
Quote:
Originally Posted by Rotary Afterfire
ok, since Im going to be fabricating kind of based on what you have, I was interested in what you were going to do to remedy the diaphragm problem. Perhaps bringing the front w/g forward off the runner towards the headlights and extending the dump-to-dp pipe to the same location and extending the rear w/g rearward and have it dump further down in the dp. Hopefully water-cooling will help and I can copy that too lol. Good luck.
|
I think only the rear WG was being affected though, since he mentioned it being close to the DP. I'm curious how the front is working too though.